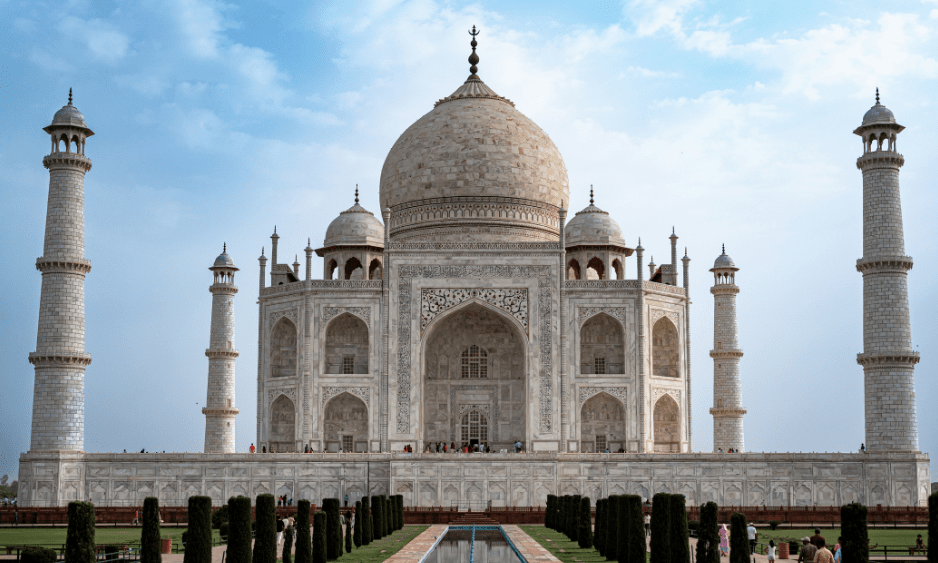
Agra: From taj mahal to footwear capital
Nestled along the banks of the Yamuna River, the city of Agra is renowned worldwide for its architectural marvel, the Taj Mahal. However, beyond its historical grandeur lies a lesser-known yet equally impressive story – the transformation of Agra into a bustling footwear manufacturing hub. Let’s delve into the journey of how this city stepped into the limelight of the global footwear industry.
Agra, renowned globally for the iconic Taj Mahal, has also carved a niche for itself in the footwear industry, becoming a prominent manufacturing hub. This transformation is rooted in historical craftsmanship and entrepreneurial spirit. The city’s legacy in leatherwork dates back centuries, with artisans honing their skills through generations. Agra’s strategic location, near major leather-producing regions and transportation routes, facilitated the growth of its footwear industry. Additionally, supportive government policies and initiatives have encouraged the establishment of footwear manufacturing units, attracting investment and fostering innovation. The availability of skilled labor at competitive costs further boosted Agra’s appeal to footwear manufacturers. Over time, the city has leveraged its rich heritage, infrastructure, and workforce to emerge as a vital player in the global footwear market, supplying high-quality products to domestic and international markets alike.
Furthermore, Agra’s ascent as a footwear manufacturing hub can be attributed to its adaptability and responsiveness to evolving market demands. The local industry has embraced modern technology and production methods, enhancing efficiency and product quality. Collaborations with international brands and manufacturers have facilitated knowledge transfer and access to global markets, elevating Agra’s status in the industry. Moreover, the presence of specialized clusters and industrial zones dedicated to footwear production has streamlined supply chains and provided a conducive environment for growth. Agra’s reputation for craftsmanship and attention to detail has earned it recognition as a center of excellence in footwear manufacturing. As the industry continues to evolve, Agra remains poised to capitalize on its strengths and maintain its position as a leading destination for footwear production.
Why Agra?
- Heritage: Agra’s rich heritage in shoemaking sets it apart as a preferred destination for footwear manufacturing. The city’s legacy, coupled with its skilled workforce, creates a conducive environment for the industry to thrive.
- Cost Efficiency: The availability of abundant raw materials and relatively low labor costs make Agra a cost-effective destination for footwear production. This competitive advantage enables manufacturers to offer high-quality products at competitive prices, driving demand in both domestic and international markets.
- Strategic Location: Agra’s strategic location in close proximity to major consumer markets, including Delhi and Mumbai, enhances its appeal as a manufacturing hub. The city’s connectivity via road, rail, and air facilitates efficient transportation of goods, further bolstering its competitive edge.
- Government Support: Recognizing the potential of the footwear industry, both the central and state governments have implemented favorable policies and incentives to encourage investment and growth. This support has played a pivotal role in propelling Agra’s footwear sector onto the global stage.
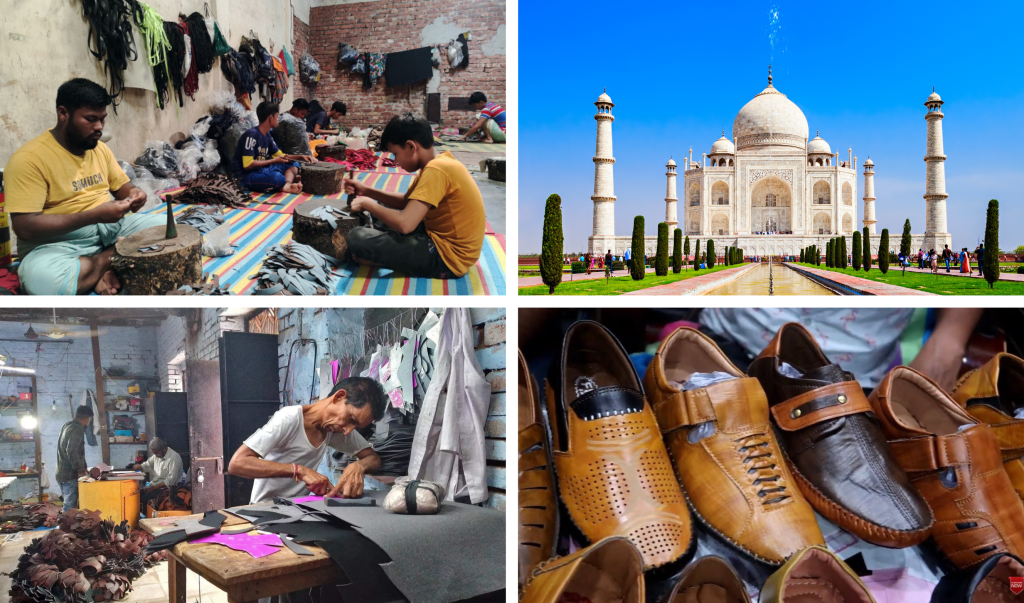
Statistics?
Production Powerhouse:
- 4 crore pairs of shoes produced annually, making Agra a national leader in footwear production.
- 2.2 crore pairs are chappals and sandals, showcasing Agra’s strength in casual footwear.
Employment Engine:
- 32,035 units across Agra and surrounding areas, employing an estimated 4.35 lakh people.
- Home-based units play a significant role, with 4,500 units contributing to the workforce.

Key Components:
- Nine mechanized last making factories produce 1,500 pairs of last per day.
- 20-30 small units add another 1,000 wooden lasts daily.
- 200 sole making units churn out 4 lakh pairs of PU, PVC, and TPR soles daily.
- 20 modern factories cater to the insole needs of the industry.
Market Reach:
- 500 traders in Hing-Ki-Mandi deal with complete shoes, primarily for the domestic market.
Additional Notes:
- Jatavs form the majority of the workforce, with a smaller presence of the Muslim community.
- Skilled workforce is estimated at 3.5 lakh.
- Production per day reaches around 2 lakh pairs.